Quality Management in Manufacturing: A Guide to Ensuring Excellence
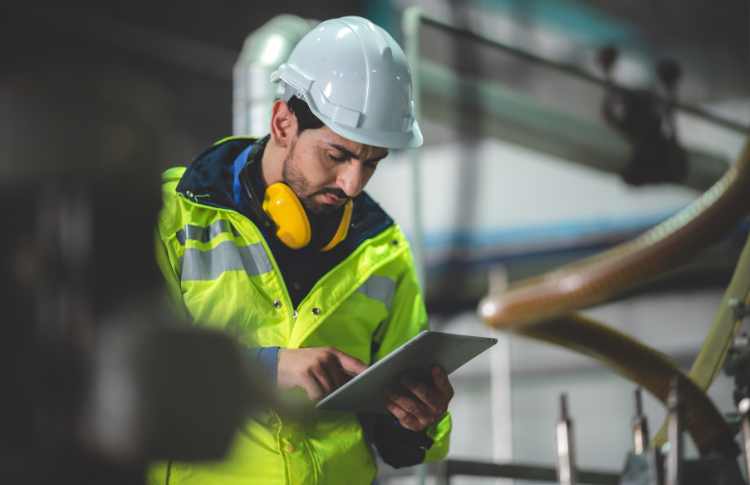
Quality is a critical factor in the manufacturing industry as it has far-reaching impacts on various aspects of a business. Beyond simply meeting product specifications, quality influences the overall reputation of a company, customer satisfaction levels, operational efficiency, and ultimately, profitability.
The Importance of Quality in Manufacturing: Why It Matters
Reputation and Customer Satisfaction: Consistently delivering high-quality products builds trust and credibility among customers. It establishes a positive reputation for the company, leading to customer loyalty and repeat business. Satisfied customers are more likely to recommend the products to others, contributing to business growth.Operational Efficiency: Quality management plays a significant role in streamlining manufacturing operations. By focusing on quality, organisations can identify and address process inefficiencies, bottlenecks, and defects. This leads to reduced waste, increased productivity, and improved overall efficiency in the manufacturing process.
Cost Reduction: Poor quality can lead to costly consequences such as rework, scrap, customer returns, and warranty claims. By emphasising quality management, organisations can proactively identify and address potential quality issues, reducing the occurrence of defects and associated costs. Investing in quality upfront can save significant expenses in the long run.
Competitive Advantage: In today's competitive market, customers have numerous options to choose from. Organisations that consistently deliver high-quality products have a competitive edge. Quality can differentiate a company from its competitors and attract customers who value reliable and superior products. It can become a unique selling point that sets the company apart.
Quality Management Systems: Key Components and Best Practices
To ensure consistent quality throughout the manufacturing process, organisations implement quality management systems (QMS) that encompass several key components and best practices.
Standardised Standard Operating Procedures (SOPs): SOPs define the standard processes and procedures to be followed at each stage of manufacturing. They establish guidelines for quality control, ensuring consistency and adherence to predetermined standards.Integrated Workflows: Effective QMS integrates quality management into the entire manufacturing workflow, from raw material procurement to final product delivery. This integration ensures that quality considerations are embedded at every step, minimising the risk of defects or inconsistencies.
Supplier Quality Management: Organisations must collaborate closely with suppliers to maintain consistent quality. Supplier quality management involves establishing quality requirements, conducting supplier evaluations, and fostering partnerships based on quality standards. This helps ensure that suppliers deliver materials or components that meet the required quality specifications.
Equipment Management Processes: Equipment used in manufacturing directly impacts product quality. Implementing effective equipment management processes, including calibration, maintenance, and periodic inspections, ensures that the machinery functions optimally and produces high-quality outputs.
Cost of Quality (CoQ) or Cost of Poor Quality (COPQ): CoQ or COPQ refers to the total costs associated with ensuring and maintaining quality, as well as the costs incurred due to poor quality. By measuring and analysing these costs, organisations can identify areas for improvement, allocate resources effectively, and make data-driven decisions to optimise quality management efforts.
Continuous Improvement: Driving Quality at Every Stage
Continuous improvement is a fundamental principle of quality management that aims to enhance quality at every stage of the manufacturing process. It involves the following key aspects:
Methodologies such as Six Sigma: Six Sigma is a data-driven approach that focuses on reducing defects and process variations. It involves the use of statistical tools and techniques to identify and eliminate sources of errors or inconsistencies, driving quality improvement.Quality Metrics: Organisations establish and track quality metrics to monitor performance and identify areas for improvement. These metrics may include customer satisfaction ratings, defect rates, supplier performance, internal process metrics, and design for manufacturability. By regularly measuring and analysing these metrics, organisations gain insights into their quality performance and can take corrective actions as needed.
Digital Transformation and Technologies: Embracing digital transformation and leveraging technologies like artificial intelligence (AI) and machine learning (ML) can revolutionise quality management in manufacturing. These technologies can automate data collection and analysis, predict and prevent quality issues, enable real-time monitoring, and facilitate proactive decision-making for continuous improvement.
In conclusion, quality management is a vital aspect of manufacturing that affects various aspects of a business. By understanding the importance of quality, implementing effective quality management systems, and driving continuous improvement, organisations can ensure excellence in their manufacturing processes. This commitment to quality can lead to enhanced customer satisfaction, improved operational efficiency, cost reduction, and a competitive advantage in the market.
Ensure your team is made up of quality employees, work with Optima to find the people you need to help your business succeed.
Please complete the form below, your data is processed here under legitimate interest. Please also note that for your privacy no data from this form is stored in this website (view our privacy policy).